In modern footwear manufacturing, the cold cement shoe production process is highly favored for its efficiency, environmental friendliness, and cost-effectiveness. This method not only simplifies the traditional shoe-making process but also enhances the comfort and durability of footwear products.
Advantages of the Cold Cement Shoe
The cold cement process does not require baking the upper into an oven to bond it with the sole, which is a stark contrast to the traditional vulcanization process. It uses water-based solvents and PU cement to firmly adhere the lasted upper to the sole, thus avoiding the high-temperature curing process. This saves energy and reduces production costs.
Cold Cement Shoe Production Process Flow
During the cold cement shoe assembly process, you can prepare the upper part of the shoe with a Strobel insole. The outsole covers the upper edge of these running shoes, making them more flexible and lightweight. Throughout the process, the last is inserted and pulled tight.
Surface Primer and Adhesive Coating
Once the upper shell is complete, the outsole unit receives a coating of cement and surface primer. The outsole is treated with a special primer designed for EVA and rubber. Additionally, the upper part of the shoe is prepared with its own specifically designed primer and cement.
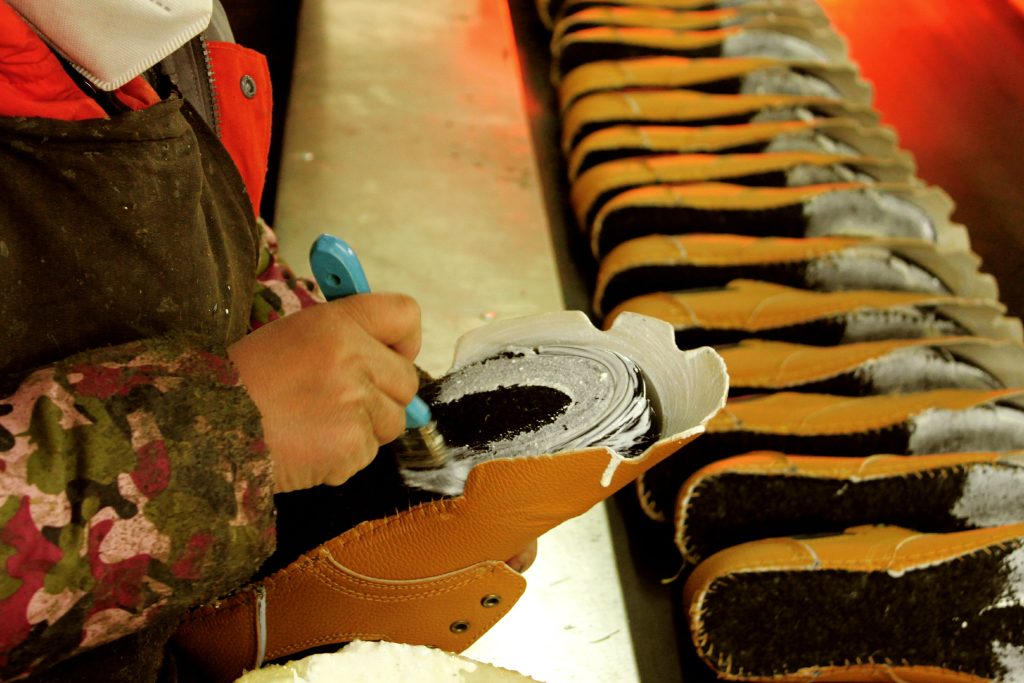
Pressing Process
Typically, shoes undergo three pressing operations with one machine. These ensure there is no gap between the outsole and the upper and that there is full contact between them. Once the shoes are pressed together, they are placed in a cooling tunnel to cure the adhesive. After the cooling tunnel, a shoe de-lasting machine is used to remove the last without wrinkling the upper.
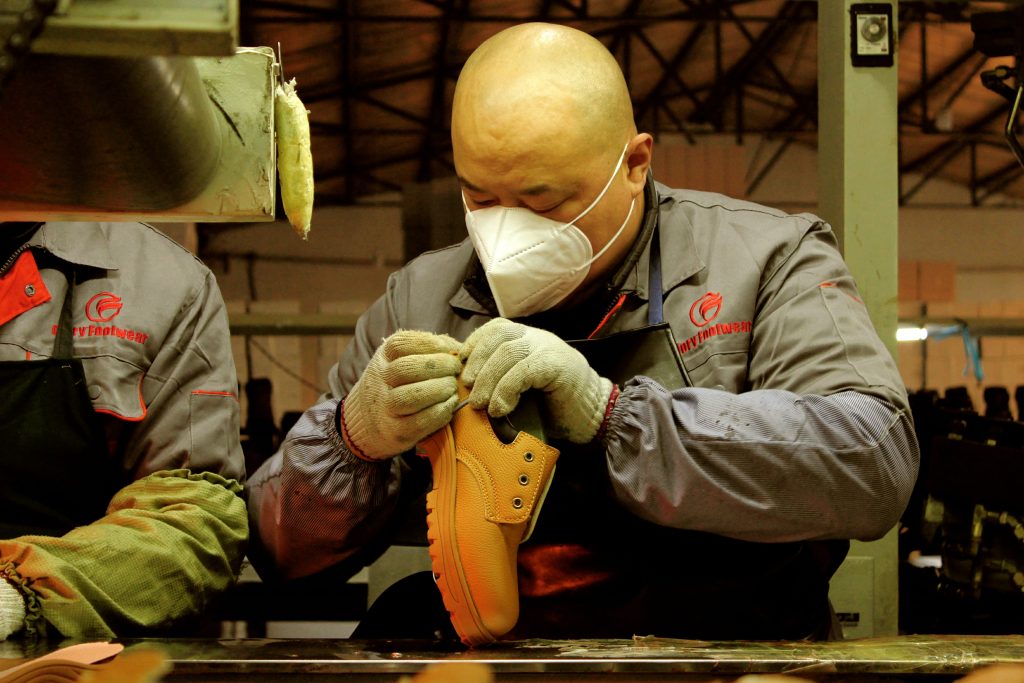
Application in Modern Footwear Industry
The cold cement shoe production process is widely adopted for its efficiency, environmental friendliness, and cost-effectiveness. Many well-known brands, such as Adidas, use this process to produce high-performance sports shoes. The cold cement process makes footwear lighter, more comfortable, and with a shorter production cycle, making an important contribution to the development of the modern footwear industry.